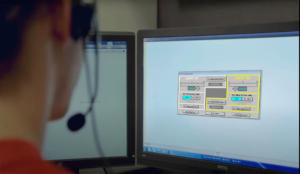
Rotoline: referência em atendimento personalizado e inovação no mercado
Reading Time: 3 minutes
A Rotoline é responsável pela fabricação e assistência técnica de máquinas de rotomoldagem inovadoras e revolucionárias para o mercado plástico. A empresa, que está no mercado mundial há mais de 20