In the current panorama of the industry industry, innovation and technology emerge as protagonists in creating a more efficient and sustainable future. Rotomolding, a process used in the manufacturing of automotive rotomolded components, lies at the heart of this transformation. This article aims to unravel the technical benefits and efficiency provided by rotomolding in creating automotive parts, from Rotomolded Plastic Interior Panels to Rotomolded Fuel Tanks, which are true landmarks of innovation.
Delving into Innovations in Automotive Rotomolding, we will explore how the solutions provided by this method not only enhance the durability and resistance of parts but also contribute to the energy efficiency of vehicles, thanks to the use of Lightweight Plastic Solutions for Vehicles. Get ready for a journey through the paths that rotomolding paves in the automotive sector.
Rotomolding in the Automotive Industry
As the flights of innovation take off in the automotive universe, rotomolding has been the pilot of various significant transformations. The process, which is already a veteran in the manufacturing of Plastic Accessories for Cars, now conquers previously unimaginable territories, becoming essential in the production of automotive parts.
This molding technique, which involves heating plastic powder inside a rotating mold, results in components of uniform thickness and without seams, which is a major advantage in terms of durability and resistance in automotive parts. But what really puts rotomolding on the podium of the industry's preferred techniques is the design freedom it offers, allowing the creation of complex and unique parts.
The importance of rotomolding is directly linked to the choice of a partner who understands cutting-edge machinery, such as Rotoline. A robust and experienced manufacturer is crucial to ensure that every curve in the parts is as precise as the demands of the automotive sector. After all, when we talk about Thermal Protection for Automobiles and Molding of Structural Parts for Cars, there is no room for error.
In summary:
- The rotomolding process offers versatility and complexity of design, perfectly adapting to the specifications of each automotive part.
- The technique ensures exceptional uniformity , resulting in parts without internal stresses, which is essential for components that cannot fail under pressure.
- Cost savings are evident, as the rotomolding process minimizes material waste and allows the use of recyclable materials, walking hand in hand with sustainability, highly valued in the current scenario.
When it comes to Plastic Parts for Vehicles, rotomolding is the technology that has revolutionized the manufacturing of these parts, capable of meeting the demands of a market constantly searching for innovation. The automotive sector, which has always been a fertile ground for technological evolution, now benefits even more from the possibilities that rotomolding provides.
It is a method that combines the technical precision demanded by the automotive market with the flexibility necessary for the creation of components that not only complement but also improve the performance and safety of vehicles. Rotomolding not only shapes plastic but also the expectations of an ever-evolving industry.
Durable Interior Components: A Technical Approach
The core of innovation in automotive design often lies in its most hidden parts - specifically, in the internal components that keep everything running smoothly. With the Rotomoldingtechnique, these parts not only fulfill their essential functions but also do so with a durability that defies time and road adversities.
Employing high-tech processes, such as those offered by Rotolinemachines, rotomolding stands out in the manufacture of plastic internal components for several reasons. Firstly, the versatility of molded plastic allows for the creation of complex parts that fit perfectly into increasingly innovative automotive designs. This is crucial, considering the complexity of current vehicle systems.
- Inherent corrosion resistance, reducing the need for maintenance.
- Superior insulation, contributing to a quieter driving environment.
- Design flexibility, allowing the integration of multiple functions into a single part.
Practical examples
For example, the dashboard and central consoles are stars of the vehicle's interior, where aesthetic precision aligns with functionality. Rotomolding, with its ability to shape plastics into complex forms, allows these components not only to host the technology necessary for vehicle operation but also to exhibit a refined finish.
In addition to visual appeal and design, durability is one of the strengths of rotomolding. Parts produced by this process have an impressive lifespan due to their resistance to wear and ability to withstand high temperatures and chemicals such as oils and fuels. This longevity is economically attractive, as parts that last longer reduce replacement costs for vehicle owners.
The automotive sector has already recognized these benefits and adopted rotomolding for the production of various parts, including airboxes, battery trays, ventilation ducts, and even components of the HVAC system (Heating, Ventilation, and Air Conditioning). Each of these parts, while lightweight, offers the robustness required for the demanding environment under the hood of a car.
Therefore, when selecting the rotomolding technique for vehicle internal components, manufacturers are choosing a path that ensures not only a revolution in quality and performance but also a commitment to long-term efficiency.
Fuel Tanks: Innovations in Safety and Efficiency
Fuel tanks represent a critical component in a vehicle's architecture, not only for storing the fuel necessary for its operation but also for being key elements in the safety and energy efficiency of the vehicle. Rotomolding, a manufacturing technique that has gained strength in the automotive industry, has been crucial in the development of innovative, safe, and efficient fuel tanks.
With rotomolding, fuel tank manufacturing reaches a high level of quality, resulting in a final product with fewer seams and, therefore, less susceptibility to leaks. Safety is one of the pillars of the revolution provided by this technology, especially when considering the stringent regulations governing the automotive sector.
- Corrosion Resistance: Unlike metallic tanks, rotomolded tanks do not suffer from corrosion problems, significantly extending their lifespan.
- Flexible Design: The versatility of rotomolding allows the creation of tanks with complex shapes, maximizing the use of available space in the vehicle.
- Reduced Weight: The use of specific polymers results in lighter tanks, contributing to the overall weight reduction of the vehicle and, consequently, to the improvement of energy efficiency.
Possibility of multilayer manufacturing
Other innovations include the development of multilayer systems, which further increase safety by preventing the emission of fuel vapors into the atmosphere. These advances in the manufacture of rotomolded fuel tanks are a direct response to contemporary demands for safer and less polluting vehicles.
From an efficiency perspective, the lightness of rotomolded tanks contributes to fuel consumption reduction. Lighter vehicles require less energy to move, resulting in lower fuel consumption and, by extension, reduced emissions of polluting gases. This virtuous cycle demonstrates how rotomolding not only aligns with the needs of the automotive industry but also with the expectations of a society increasingly conscious of environmental issues.
Advantages of Rotomolded Fuel Tanks:
- Enhanced safety against leaks and ruptures.
- Possibility to create innovative designs that fit perfectly into available spaces.
- Positive impact on vehicle energy efficiency due to reduced weight.
- Contribution to environmental sustainability thanks to lower pollutant emissions.
In the face of so many benefits, the choice of a rotomolding machines like Rotoline is fundamental. The excellence and precision of the equipment offered ensure that fuel tanks meet the most demanding automotive specifications and raise the standard of safety and efficiency required by the market.
Therefore, it is indisputable that rotomolding has taken on a leading role in the development of automotive components, particularly concerning fuel tanks. The innovations brought by this technique have positively impacted the industry, bringing technology and innovation to the forefront of discussions about the production of cutting-edge automotive parts. With rotomolding, the revolution in safety and efficiency is a constantly evolving reality.
Lightweight Materials: Their Role in Vehicle Energy Efficiency
The relentless pursuit of more efficient vehicles has led the automotive industry into a true technological ballet, where each component plays a fundamental role in the overall performance. In the current scenario, lightness has become a star dancer, and lightweight materials produced by the Rotomolding process are ideal partners in this energy choreography.
- Reduction in the total weight of the vehicle, contributing to fuel consumption and emissions of polluting gases.
- Use of advanced polymers capable of combining lightness and strength, showing that robustness does not necessarily need to weigh on the scale.
- Parts such as bumpers, panels, and reservoirs produced with these materials demonstrate how rotomolding is synonymous with functional innovation.
In a world where every drop of fuel and every gram of CO2 counts, the application of lightweight materials from rotomolding in the automotive industry is a giant step toward a greener and more efficient future. With Rotoline, this future is not just a dream; it is a constantly moving reality.
Production Process: How Rotomolding Meets Automotive Specifications
When we delve into the world of automotive parts manufacturing, we encounter a cast of technical requirements that more resemble a labyrinth of precision and quality. In this scenario, rotomolding, emerges as a beacon of efficiency, navigating with mastery through the waters of automotive sector requirements.
Meeting Strict Technical Standards
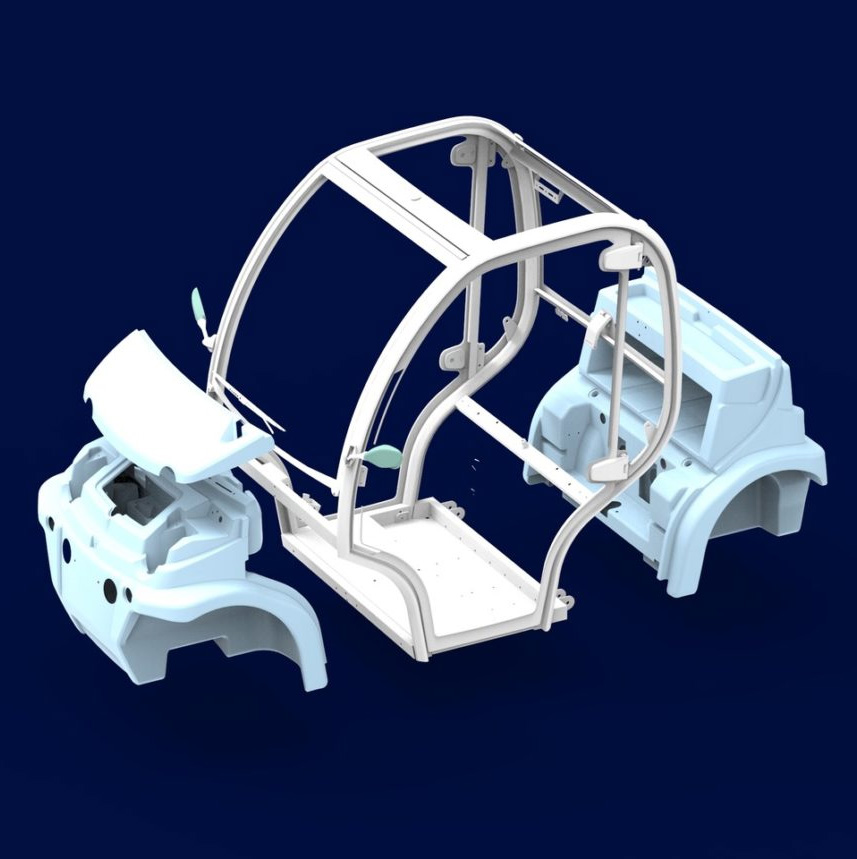
- The manufactured components must comply with internationally established safety and performance standards, such as the rules set by the Brazilian Association of Technical Standards (ABNT), in the aforementioned NBR 7505. Or even the American Petroleum Institute (API), used as a parameter in the United States and as reference around the world.
- Rotomolding, with its ability to create uniform and stress-free components, ensures that each part meets the stipulated standards.
Precision in Every Curve
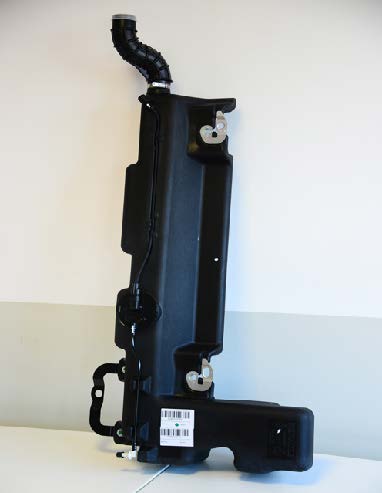
- The complex geometry of certain automotive parts is not an obstacle for rotomolding. Rotoline machines are designed to faithfully reproduce the intricate shapes necessary for specialized automotive components.
- This is possible thanks to the versatility of the process, allowing the molding of parts of various dimensions and shapes, respecting the specifications with almost artisanal precision.
Visible and Tangible Quality
- In the automotive industry, quality is palpable. Rotomolding promotes a uniform texture and high-standard finish, elements that align with the industry's constant pursuit of aesthetic and functional excellence.
- With rotomolding, surface defects are minimized, resulting in parts that not only perform their functions efficiently but also contribute to the visual appeal of the automobile.
Through the rotomolding process, Rotoline manages to achieve a synergy between adaptability and precision, resulting in parts that not only meet automotive specifications but often exceed them. This is crucial in an industry where the margin for error is minimal, and the demand for innovation is constant. The technique also allows automotive engineers to design and adjust their specifications knowing that there will be a manufacturing process worthy of their creative and technical aspirations.
With rotomolding, the automotive industry finds not only an ally in the production of durable and safe parts but also a sustainable path to innovation in design and functionality. Rotoline machines are the instruments that make this journey possible, reflecting a commitment to the quality and satisfaction of the complex needs of the automotive sector. With each piece produced, the ability of rotomolding to meet the challenges of contemporary automotive production is reaffirmed.
Impact Resistance: Protecting Passengers with Rotomolded Parts
The ability to absorb and dissipate energy resulting from impacts is one of the pillars of vehicle safety. This is where rotomolding, with its versatility and precision, acts as a true protective shield for passengers. Rotoline understands that each manufactured component carries the responsibility of protecting lives, making impact resistance a non-negotiable priority.
Rotomolded parts have a uniform distribution of weight and density, making them ideal for absorbing shock without compromising structural integrity. Let's explore how this translates into safety:
Structural Uniformity:
The rotomolding technique ensures that parts have walls without residual stresses, which is essential for the part to maintain its shape and effectiveness under impact.
Designed Flexibility:
Unlike rigid materials that can shatter, plastic parts produced by rotomolding allow a certain degree of flexibility that absorbs and distributes the force of the impact.
Design Integration:
Rotomolding allows the manufacturing of complex parts in a single step, eliminating weak points that would be introduced by seams or fixations.
To illustrate the success of Rotomolding in producing parts with high impact resistance, let's look at concrete examples:
- Automotive bumpers manufactured by the rotomolding process offer superior protection, dissipating the energy of the impact and minimizing damage.
- Energy absorption parts strategically located in the vehicle body help protect occupants in case of collisions.
These examples highlight the importance of the chosen material and process in the manufacture of automotive parts. It is worth noting that Rotoline strives for continuous innovation, resulting in increasingly safe and reliable parts. Rotomolding not only meets but often exceeds the stringent safety standards of the automotive industry.
Ultimately, the adoption of rotomolded parts goes beyond functionality or aesthetics; it touches the core of automotive safety. The choice of high-quality processes and materials, such as those provided by Rotoline, is an investment in passenger protection and the construction of a legacy of trust and excellence.
Sustainability in the Production of Automotive Parts: A Technical Perspective
Sustainability has become a keyword in the modern automotive industry. With technological evolution and growing environmental awareness, the sector has sought innovations not only to increase vehicle efficiency but also to minimize the environmental impact of automotive parts production. In this context, Rotomolding emerges as a technical solution aligned with sustainability precepts, combining production efficiency with ecological responsibility.
The Rotomolding used by Rotoline allows the manufacturing of automotive parts with precise control over material usage. This results in reduced waste in production, as the technique allows the exact amount of plastic to be used to form the part, without unnecessary leftovers.
Sustainable Advantages of Rotomolding
- Material usage efficiency: Rotomolding allows optimized use of plastic, resulting in less waste and greater recyclability of production leftovers.
- Emission reduction: Automotive parts manufacturing processes by rotomolding have a lower carbon footprint compared to traditional methods, contributing to a decrease in greenhouse gas emissions.
- Longevity of parts: The durability of rotomolded parts implies fewer replacements and, consequently, less demand for resources and energy for new parts.
Additionally, the technical aspect of rotomolding allows the creation of complex designs and parts with intricate geometries without the need for multiple production stages, thus reducing energy and resource consumption during the manufacturing process.
Rotomolding and Circular Economy
One of the pillars of sustainability in the industry is the integration of production processes into the concept of the circular economy. In this model, the end of the useful life of a product does not mean disposal but rather the starting point for a new production cycle. Rotomolding operates in harmony with this philosophy, as automotive parts produced by this process are entirely recyclable. This allows, after the product's life cycle, the material to be reprocessed and molded into new parts, closing the production cycle and minimizing environmental impact.
Partnerships for a Sustainable Future
By choosing a reputable rotomolding machine manufacturer like Rotoline, automotive parts manufacturers can not only fulfill their legal and ethical obligations regarding sustainability but also strengthen their brands with environmentally conscious consumers. Such partnerships are essential to drive innovations that respect the limits of our planet without compromising the quality and safety of vehicles.
In summary, rotomolding represents a bridge between technological innovation and environmental responsibility in the production of automotive parts. By reducing waste, lowering emissions, and promoting circular economy principles, Rotoline and rotomolding demonstrate that it is possible to align the need for progress in the automotive sector with the imperative to preserve the environment for future generations.