Introduction
Imagine a world where hospital equipment is as adaptable as a chameleon, changing and evolving to meet the specific needs of each medical environment. Welcome to the era of rotomoulded medical equipment, the technique that is transforming the healthcare sector with its ability to create customized designs that fit seamlessly into hospitals' demands. Rotomoulding is not just about practicality. It's efficiency in its purest form, allowing the manufacturing of durable and lightweight parts that are easy to handle and maintain. This article will explore the universe of applications and benefits of rotomoulding in healthcare, revealing how this process can be the key to faster and safer hospital care.
ROTOMOULDING: WHAT IS IT AND HOW DOES IT WORK
A Rotomolding is an industrial process where the plasticity and versatility of plastic meet science to create robust and complex products. It's no different in medicine, where this technique has revolutionized the production of hospital equipment. But what exactly is rotomoulding and how does this technology that is becoming so vital to hospital practicality work?
The rotomoulding process, or rotational moulding, begins with fine plastic powder placed inside a mould. This mould is then heated and simultaneously rotated around two axes. The plastic melts and spreads, adhering to the inner walls of the mould, thus forming the desired part. After cooling, the product acquires the necessary strength and shape to face the day-to-day challenges in hospitals.
This manufacturing technique brings unique characteristics that are particularly valuable to the hospital environment, such as chemical resistance and durability. ICU equipment ,for example, needs to withstand constant exposure to strong cleaning and disinfecting products without compromising the material's integrity. Rotomoulding ensures that these life-saving tools not only survive but thrive under such conditions.
POSITIVE POINTS OF ROTOMOULDED MEDICAL EQUIPMENT
- A Design flexibility is another major advantage of rotomoulding. It allows creating complex shapes and anatomical designs that adapt to healthcare professionals' needs without increasing production costs.
- The uniformity of the walls of rotomoulded products eliminates weak points, allowing them to withstand pressures and frequent impacts in such a dynamic environment as healthcare.
- Furthermore, the possibility of incorporating materials with specific properties, such as plastics with antimicrobial additives, broadens the spectrum of use of rotomolded equipment regarding hospital hygiene.
Although rotomoulding may seem like a simple process, its application in medicine is complex and requires a high level of precision. Each mould must be carefully designed and created to meet the exact needs of medical equipment, which must comply with strict hospital standards and obtain medical certifications before being used.
In this way, rotomoulded medical equipment is not just a matter of mass production. But also an exercise in innovation and engineering, aiming to improve and facilitate care and operations in hospitals. It's a perfect synthesis between form and function, material and need, science, and health.
CHEMICAL RESISTANCE AND DURABILITY IN THE ICU
The Intensive Care Unit (ICU) is a critical environment, where every minute is essential. Each ICU equipment plays a crucial role, being fundamental to face challenges. Rotomoulded medical equipment is the technology that allows these equipment to perform impeccably.
Understanding the gravity of the hospital scenario, chemical resistance and durability are leading attributes that make a difference. Equipment produced through rotomoulding has a "chemical armor" that makes them resilient in the face of aggressive disinfectants and the constant battle against infectious microorganisms. This is essential because the ICU is a territory where pathogens are always lurking, and sanitization is a relentless routine.
Furthermore, it is in this high-pressure scenario durability of rotomoulded equipment comes into play. They must withstand continuous use and excessive handling without failing or compromising their functionality. In an environment where every second counts, equipment reliability is a pillar that sustains life.
- Resistance to a wide range of chemical substances used for cleaning and disinfection.
- Smooth and non-porous surfaces that prevent bacterial adhesion and facilitate cleaning.
- Robust structures capable of supporting weight and constant use without deforming or breaking.
THE IMPORTANCE OF ROTOMOULDING IN MEDICAL EQUIPMENT IN THE ICU
These characteristics result from a meticulous Rotomoldingprocess that molds plastics to perfection, resulting in homogeneous surfaces free from fissures that could harbor pathogens. Moreover, rotomoulding allows the incorporation of antimicrobial additives directly into the material, further enhancing patient and healthcare professional safety.
When considering success stories, we see that ICU equipment created with this technology has already proven its effectiveness. From respirators and monitors to beds and emergency carts, rotomoulding offers a comprehensive solution that combines high performance with hospital practicality work.
In summary, choosing rotomoulded equipment for the ICU is an investment in safety and the effectiveness of critical care. Rotomoulding in the medical field is not just an innovation; it is a silent ally in the daily battle for life, ensuring that healthcare professionals have by their side equipment that does not fail when needed most. After all, in the ICU, equipment quality can be the thin line between hope and uncertainty, and rotomoulding ensures that this line is strong and unshakeable.
ANATOMICAL DESIGN AND HOSPITAL PRACTICALITY
Imagine a technology capable of shaping the future of healthcare, where every curve and contour of hospital equipment is designed to fit perfectly to the human body. This is the promise of rotomoulding. A manufacturing technique that allows the creation of customized designs that not only fit like a glove in human anatomy but also enhance practicality and efficiency in the hospital environment.
With the ability to produce seamless parts with smooth contours, this technique is the key to manufacturing equipment that communicates with space and human touch, allowing doctors and nurses to perform their tasks with greater agility and precision.
WHAT TYPES OF EQUIPMENT CAN BE MANUFACTURED?
Equipment such as ergonomic stretchers, wheelchairs, and even neonatal cribs gain a new dimension of comfort and safety. For example, a rotomoulded stretcher can offer perfectly contoured surfaces that reduce the risk of injuries during patient transport, as well as being incredibly lightweight and easy to handle. This combination of factors benefits not only patients but also provides healthcare professionals with a new perspective on operational efficiency.
- Stretchers with anatomical design that minimize patient discomfort and facilitate transport
- Lightweight, durable wheelchairs adapted to specific user needs
- Neonatal cribs designed to offer maximum safety and comfort to newborns
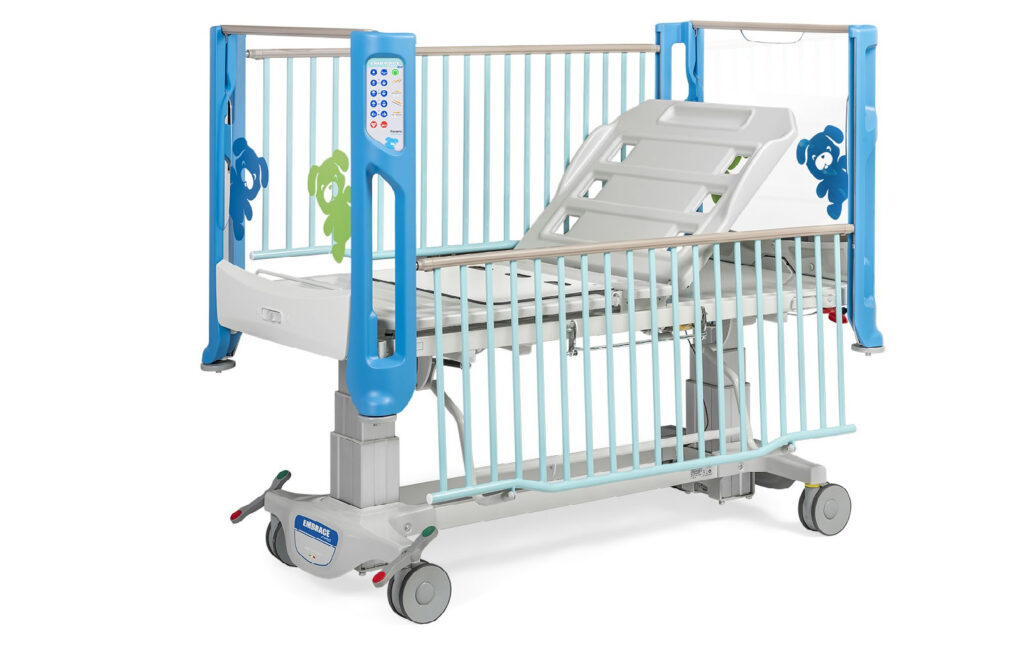
These are just some examples of how rotomoulding is revolutionizing the design of medical equipment, providing solutions that embrace the human form and medical practice with efficiency and care. With the rise of this technique, the future of hospitals is becoming more human, more practical, and undoubtedly more innovative. It is the science of caring meeting the art of creating. Where each moulded piece is a step towards a more welcoming and efficient care.
For more information about rotomolding and its impact on the hospital industry, explore the resources available on the Issuuplatform, where publications like "Revista Hospitais Brasil" offer a glimpse into the latest innovations and trends in the healthcare sector.
Radiological Technology and Innovation in Rotomolding
A Radiological technology finds an invaluable ally in the Rotomolding process. It is not just about creating equipment; it is about reinventing and improving the way medicine visualizes and understands the human body.
Rotational molding allows the manufacture of large and complex geometric pieces, essential characteristics for radiological equipment. Such equipment demands not only innovationbut also a design that allows for its intuitive and safe operation, integrating perfectly into the hospital environment.
The impact of this methodology on the development of Radiological technology is remarkable. By promoting the production of unique pieces, without welds or seams, rotational molding ensures a continuous surface, which is vital for the cleaning and maintenance of hospital hygiene. In addition, the structural uniformity offered by the process guarantees that the equipment has the durability necessary to withstand the fast-paced daily life of health institutions.
- Rotational molding allows the execution of complex designs, which is essential for the ergonomics and handling of radiological equipment.
- The materials used provide adequate X-ray attenuation characteristics, allowing the quality of radiological images not to be compromised.
- The monolithic construction of the components reduces the risk of contamination, as there are no gaps or spaces where microorganisms can proliferate.
Exploring the horizon of possibilities, radiological technology driven by rotational molding is transformed into a pillar of trust and precision. Tomographs and magnetic resonance imaging equipment are brilliant examples of how innovation permeates the medical field, leveraging the quality of diagnosis and, consequently, clinical decision-making.
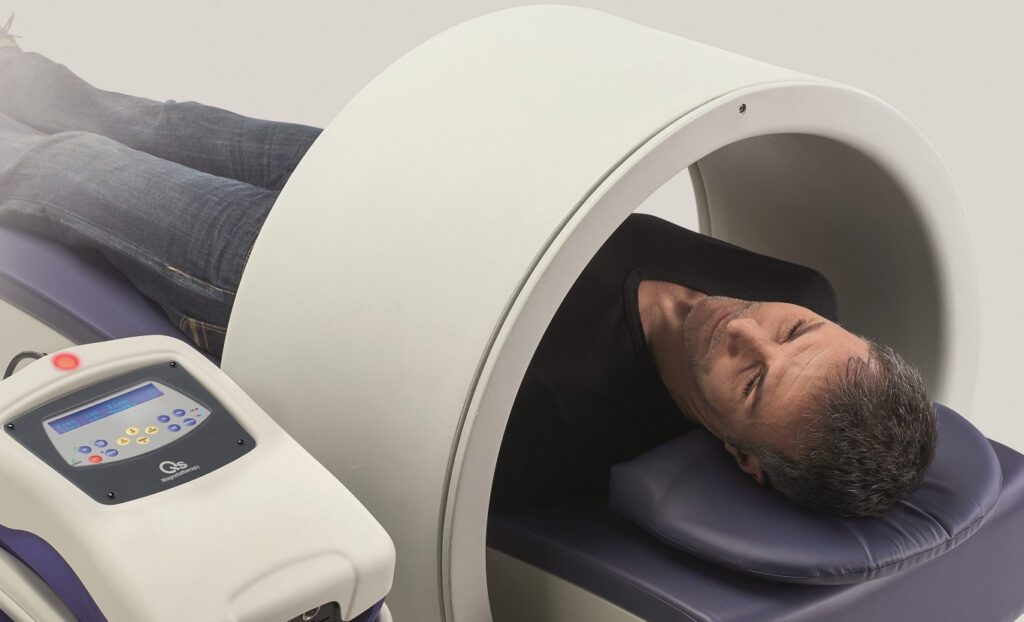
As medicine advances, rotational molding follows its pace, proving to be an innovative solution that molds not only ICU equipment but also the future of health.
ANTIMICROBIAL SURFACES AND HOSPITAL HYGIENE
When we talk about antimicrobial surfaces, we refer to the ability of a material to inhibit the growth of pathogenic microorganisms. Rotational molding can incorporate antimicrobial additives into the plastic compound itself before it is molded. This results in surfaces that, by their very nature, are hostile to the proliferation of germs.
This advance is a stronghold in the prevention of hospital infections, which are great villains in the recovery of patients and can have devastating consequences. Equipment such as hospital beds, procedure trays, and even toys in pediatric wards can benefit from this technology. The presence of antimicrobial surfaces on these objects means one more barrier in the fight against cross-contamination, one of the main modes of transmission of infections in healthcare environments.
- Hospital beds with antimicrobial surfaces become less likely to harbor bacteria, even between regular cleanings.
- Procedure trays that resist attack by microorganisms ensure that instruments remain in a more controlled environment.
- Toys and equipment in pediatric areas protect little patients, whose immune systems are often more vulnerable.
The adoption of rapid ATP cleaning verification tests by providing immediate data on the presence of contamination. Thus, hospital managers can not only trust the protection incorporated into the equipment but also monitor and adjust cleaning protocols with surgical precision. Maintaining the hospital environment at its maximum safety capacity.
By repelling microorganisms before they even establish themselves, antimicrobial surfaces are true sentinels in protecting patient health and the efficiency of medical care.
MEDICAL CERTIFICATIONS AND PRODUCTION QUALITY
Rotational molding, known for its versatility and durability, adapts to meet the specific requirements of the medical sector. With the ability to create large, hollow, and complex geometric parts, it proves to be a superior choice for the manufacture of items such as medical toolboxes and emergency equipment.
It is not just a process; it is a promise of compliance and excellence. By using linear low-density polyethylene (LLDPE), endowed with characteristics such as high impact and corrosion resistance, resistance to extreme temperatures, and durability, the equipment produced is ideal for the medical setting, where hygiene and efficiency are paramount.
Examples of certifications and standards met by rotational molding include, but are not limited to, specifications for rescue equipmentwhere watertightness is vital, and transport boxes for sensitive materials that must be immune to dust and water. Products such as water treatment tanks and material storage containers, essential for hospital logistics, are also the result of this technology.
In summary, rotational molding is not just a manufacturing technique; it is a reliable ally in the relentless pursuit of patient safety and well-being. By shaping products that meet the most rigorous standards, it proves itself indispensable in the healthcare field, bringing innovation closer to human care.
- Compliance with international safety and quality standards.
- Use of materials such as LLDPE, which offer superior properties for medical applications.
- Production of equipment that is an integral part of hospital logistics and operation, such as specialized tanks and containers.
By walking side by side with rotomolding, the medical sector embraces a future where each piece of equipment is a testament to science applied with care and precision, a future where health and technology dance together in perfect synchrony.
EFFICIENT MOBILITY IN HOSPITAL EQUIPMENT
Healthcare professionals need instruments that not only respond with precision but also move with ease. Rotomolding comes on the scene to facilitate the work of these professionals, improving the quality of patient care.
For example, in the medical sector, rotomolding is used to create hospital beds that need to be adjusted and moved frequently. The seamless nature of the process results in a smooth surface that is easy to clean and disinfect, an advantage not only in terms of mobility but also of hygiene. In addition, the possibility of integrating functionalities, such as IV stands and monitoring equipment, simplifies the logistics around the patient's bed.
Another tangible example is the use of rotomolding in emergency carts. These four-wheeled heroes, which carry vital medications and equipment, benefit from the lightness and resistance provided by the technique, ensuring that they can be maneuvered quickly in critical situations. The adaptability of the process also allows these carts to be customized to meet the specific needs of each hospital department.
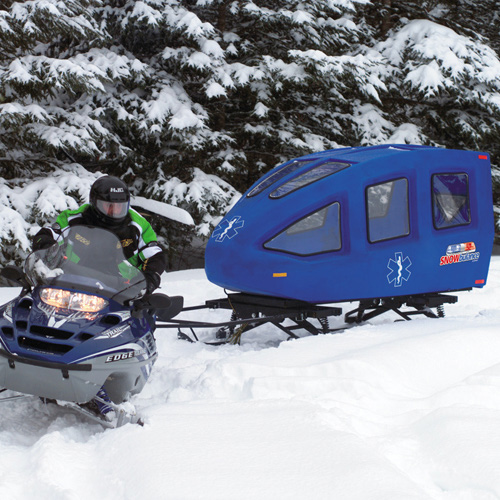
In the hospital environment, where every second counts, the efficient mobility of equipment can mean the difference between life and death. Rotomolding, therefore, is not just a matter of operational efficiency but also an invaluable ally in the race against time to save lives. And so, amidst advances and innovations, rotomolding stands out as an innovative solution that raises the standard of patient care, while silently circulating through the corridors, carrying with it the promise of a future where health and technology walk side by side.
Conclusion
As we navigate the medical sphere of Rotomolding, we unveil a world where Durability, Anatomical Design and Hospital Practicality converge for the well-being of patients and the effectiveness of healthcare professionals. Technology, intertwined with Innovation, defines paths that lead to more accurate diagnoses and faster treatments.
The Antimicrobial Surfaces are the shield against invisible threats, ensuring Hospital Hygiene. Medical certifications and Hospital Standards are the seals of guarantee, essential in the production of any equipment that values quality and compliance. The rotomolding route has guided us through landscapes of efficient mobility, essential for hospital dynamics, where every second counts in the race against time.
We conclude that rotomolding is, without a doubt, an innovative solution that meets the demands of a modern and demanding hospital setting, where each piece is a vital link in the healthcare chain.