A Rotomolding Through a study on trends and innovations for the rotomolding market, we will explore new technologies that allow for greater quality control, automation, use of sensors and Internet of Things (IoT), as well as the use of more sustainable materials, emerging prototyping technologies, and reinforced rotomolding.
What is rotational molding?
Rotomolding is a technique used in plastic material manufacturing. It is performed on a machine called a Rotomolder, which consists of a mold, a rotating axis, and a heat source.
When comparing the rotational molding technique to plastic injection molding, we observe significant differences that confer specific advantages. Rotational molding, for example, enables the creation of products with a more uniform thickness, contributing to the consistency and quality of the final item. Additionally, it stands out for the ability to provide a more refined finish, adding aesthetic value to the manufactured products.
Another notable aspect of rotational molding is its ability to provide greater resistance to temperature variations. This makes it particularly suitable for the production of parts that face adverse environmental conditions.
Thus, rotational molding not only represents an innovative technique in plastic manufacturing but also offers distinct benefits that make it a valuable choice in certain industrial contexts.
Differences
Instead of using liquid plastic injection into a mold, rotational molding utilizes plastic powder, which is inserted into the machine and heated. Afterward, we initiate the rotating axis, uniformly mixing it, and then filling the mold. When the plastic cools, we remove the product.
Evolution of Rotomolding
In recent years, rotational molding has experienced significant advancements, driving the evolution of this technique in the realms of technology and materials. Notable progress includes the continuous development of new plastic materials, providing more advanced and sustainable options for specific applications, and innovations in mold design, with the use of CAD technologies to create more complex and efficient geometries. Additionally, the enhancement of process control has allowed greater precision in production conditions, resulting in final parts with more consistent quality.
Rotational molding has also followed sustainable trends, incorporating the use of recycled materials and optimizing energy consumption. The integration of information technology has played a crucial role, enabling the monitoring and optimization of production processes. Finally, the expansion of rotational molding applications in various sectors stands out as a trend, extending its reach and usefulness in the industry. These combined advancements highlight the growing relevance and versatility of rotational molding as an innovative manufacturing technique.
Advantages of Rotomolding
This technique is flexible, efficient, and reliable, as it allows the creation of resistant and durable parts for a wide range of applications. One of the main features. advantages This technique is the relatively low manufacturing cost. Rotational molding is a low-cost process. This is because it doesn't require the use of complicated or expensive molds, and production costs tend to be lower. This is one of the reasons why it is the preferred choice for entire plastic parts.
Going beyond
Another advantage of rotomolding is that it is capable of producing complex parts that could not be manufactured otherwise. With this process, you can create parts that have slip-resistant coatings and wear-resistant coatings. Parts can also be made with windows, clips, cutouts, anchors, flanges, and even handles.
Rotational molding also stands out for its versatility, being capable of manufacturing robust parts with resistance to pressure, corrosion, and impact, while also presenting high gloss and excellent impact resistance. These characteristics give rotational molding significant applicability in both industrial and domestic contexts, making it a relevant choice for a variety of applications.
Current Challenges of Rotomolding
Rotational molding, a plastic manufacturing process recognized for its speed, precision, and more affordable cost compared to traditional methods, faces notable challenges that influence its growth in the market. One of these fundamental challenges is the limited awareness and knowledge about trends and innovations in plastic manufacturing, making rotational molding less known compared to more established methods such as plastic injection and extrusion.
This lack of awareness implies restricted access to up-to-date information about specific trends and innovations for rotational molding. Furthermore, professionals involved in this process face the need for periodic updates to ensure the incorporation of the latest technologies and methods into their practices, thus ensuring the efficient production of their products. This demand for constant updating stands out as one of the critical challenges that the rotational molding industry currently faces.
Innovations in the Rotomolding Market
As rotomolding is an affordable and high-quality manufacturing technique for plastic parts, it is increasingly sought after by manufacturers of all sizes. To enhance the efficiency of this process, trends and innovations in rotomolding are an essential resource.
Technologies
One of the key elements of innovation in rotomolding is advancements in precision molding technologies that enable manufacturers to create more complex parts compared to traditional methods. Additionally, innovation in rotomolding also includes improvements in monitoring and quality control processes to ensure higher quality of the final product.
With the growing demand for rotomolding, trends and innovations in rotomolding are crucial to ensure that manufacturers stay ahead of the competition. Investing in innovation tools such as precision molding technology, plastic modeling technology, and quality monitoring is essential to achieve the best possible results.
Complete
In recent years, rotational molding has undergone significant innovations. The increase in automation is one of the main contributing factors for it to become one of the most popular techniques in the market. Automation is the technology that enables machines to perform tasks automatically, optimizing the production process to enhance efficiency and product quality.
As a result, manufacturers are adopting automation in rotational molding. In order to improve the quality and precision of their products, manufacturers are adopting automation. The main benefits of automation include a reduction in production costs, an increase in production speed, and the ability to manufacture products with accuracy. Furthermore, automation also enables manufacturers to adhere to established quality standards in their industry.
Growing Market
In recent years, investment in automation in the rotomolding sector has significantly increased. Manufacturers have invested in automated technology to improve their production processes. For example, some manufacturers are using robots for molding operations, as well as other tasks that were previously performed manually.
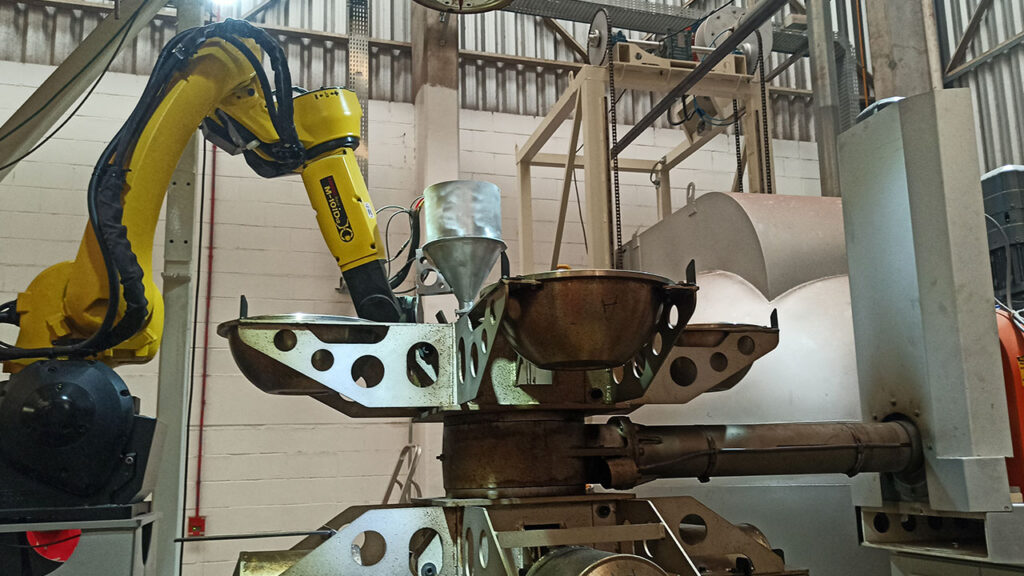
In the future, it is believed that automation will continue to play a crucial role in the rotomolding industry, enabling manufacturers to produce higher quality and more precise products. Additionally, automation will also help manufacturers reduce costs and increase productivity.
Recycled Materials
The trend of using recycled material for the production of rotomolded parts continues to grow. This trend is expected to continue expanding in the market due to increasing environmental concerns and ecologically responsible consciousness.
Pros and cons
Using recycled materials in rotomolding can be positive in many ways: it minimizes material waste and helps reduce the consumption of non-renewable raw materials.
On the other hand, parts made from recycled materials tend to have a lower durability because of the possibility of cross-contamination. Lastly, the treatment processes for recycled materials are more complex and expensive than traditional ones.
Research
However, this has been a growing demand in the rotomolding market. As a result, doors are opening to make the so-called Circular Economy, which has gained strength in research development, increasingly present in the daily operations of companies working with plastic transformation. research development, increasingly present in the daily operations of companies working with plastic transformation.
Due to these factors and others, trends and innovations for rotomolding with recycled materials are essential to develop more efficient, safe, and high-quality processes.
Reinforced Rotomolding
An emerging trend in rotational molding is the use of reinforcements to increase the strength of the finished part. These reinforcements typically consist of adhesives, fiberglass, or Kevlar. These materials enhance the robustness of the final piece, allowing its use in more demanding applications. Examples of applications include fuel tanks, water tanks, and industrial equipment. When the part is reinforced using stronger materials, it is capable of withstanding extreme loads and hardens the piece in a way that simple rotational molding cannot.
Coated Products
In addition, with trends and innovations in rotomolding, users have the ability to add coatings to rotomolded parts. These coatings offer resistance to corrosion, waterproofing, longevity, and other qualities that rotomolded parts may have. These coatings can be used to improve the corrosion resistance, durability, wear resistance, and safety of the part. Therefore, these coatings are a great way to further enhance the quality of the rotomolded part.
These coatings can be used to improve the corrosion resistance, durability, wear resistance, and safety of the part. Therefore, these coatings are a great way to further enhance the quality of the rotomolded part.
Rotomolding with Applied Coloring
It is a growing trend in the field of rotomolding. For those who wish to customize their products, rotomolding with applied coloring offers the possibility to color rotomolded products quickly and safely. Rotomolding with applied coloring is done using pigmentation or pigmentation with the addition of plasticizers during the rotomolding manufacturing stages.
Personalization
The use of this technology allows for the production of colorful products on a large scale and with consistent quality. Many rotational molding companies have implemented this trend to provide their customers with customized products and a professional finish, resulting in increased satisfaction and sales. Therefore, this is a potentially lucrative innovation that is important for any company in the rotational molding industry.
Production of Complex Parts
One of the most pronounced trends and innovations in the rotomolding market is the production of complex parts with specific characteristics for niche applications. The rotomolding process allows for the creation of parts with a wide variety of shapes and characteristics, making it ideal for this type of production. New materials also help to improve rotomolding capabilities, allowing for greater precision and strength of the produced parts.
Advancements in Prototyping
Rotomolding prototyping has developed rapidly in recent years, allowing for much faster and efficient scale production. With the development of this technology, many companies are able to save resources, accelerate the product development process, and consequently add value to their businesses.
New Materials
To keep up with these trends and innovations in rotational molding, manufacturers have been developing new materials for prototyping. The use of lightweight materials with high strength and quality finish has allowed for the creation of more sophisticated rotational molding projects, ready for large-scale production.
In addition to materials, computer graphics have helped optimize the prototyping process. By using three-dimensional models, it is possible to evaluate the product's structure even before starting the rotational molding process.
This allows for corrections and adjustments as needed to improve the product's quality.
Improvements in Molding Processes
Trends and innovations for rotomolding have offered new processes to improve the quality and efficiency of production. One of the most interesting areas for improvement in the rotomolding process is the manipulation of materials, including the development of lighter materials with better wear resistance, resistance to high temperatures, and low cost.
In addition, other improvements have been made in process automation, such as the adoption of automated quality control systems, which allows for reduced production time and increased final product quality.
Advanced technologies such as virtual reality and 3D printing are also being utilized as tools to enhance rotational molding processes.
Trends
Rotomolding is still evolving to become even more efficient today. In the midst of a scenario of constant innovation and technological development, it is important for companies to stay updated on the trends and innovations of rotomolding.
Technological growth in the industry allows for the production of new materials for the production of high strength and durability parts. Technological advances allow for the production of lighter and weather-resistant parts, as well as advanced production processes that elevate quality and final results.
Emerging Technologies
The goal of trends and innovations for the rotomolding market is to increase efficiency, reduce costs, and improve final products. There are some emerging technologies that help achieve these results.
The use of machine analytics and sensors, as well as the application of artificial intelligence, can assist in identifying issues in production, allowing for the maintenance of product quality.
Rotomolding and Automation
These are topics that, together, represent a significant leap in the field of rotationally molded products. Additionally, with new automation technologies and data control, it has been possible to enhance processes, such as data acquisition and production speed.
Trends and innovations for rotomolding also include software applications. Industrial processes are now equipped with quality control applications that enable the management of production data, performance monitoring, and necessary periodic maintenance.
New possibilities
Furthermore, innovation in the field of robotics is opening new possibilities for automation in rotational molding processes. Robots can perform tasks that require high precision and repeatability, which were traditionally done manually, thereby improving the final product's quality.
Thus, rotomolding is becoming increasingly innovative and efficient, allowing manufacturers to reduce production time and increase the quality of finished products.
Conclusion
Rotational molding has advanced in the industry, enabling the manufacturing of products in a more efficient and productive manner. What makes rotational molding even more interesting is its ability to adopt new trends and innovations for the production of customized and complex parts.
Automation, recycled materials, reinforced rotomolding, applied coloring, advanced prototyping, improvements in molding processes, and emerging technologies are making rotomolding even more competitive. In this way, companies can use these innovations to take advantage of the best that the rotomolding process has to offer, preparing for the future of the industry.