WHAT IS ROTATIONAL MOLDING
A rotomolding is a revolutionary process that allows for the creation of complex objects using plastic. The ability to create unique shapes, sizes, and textures, along with a variety of durable plastics, makes rotational molding the answer for producing customized items for any type of need.
IN THIS ARTICLE:
In this article, we will discuss the following topics: the history of rotational molding, the main industries that utilize it, and the benefits that this process offers. So, get ready to learn everything you need to know about rotational molding!
HISTORY OF ROTATIONAL MOLDING
The technique of rotational molding was first patented in 1947 by James Caldwell, an American inventor.
He developed the process for manufacturing plastic objects with a spherical shape. In the 1950s, the process was further improved by other inventors such as Richard F. Carlson and Robert B. Harrison, who added enhancements to Caldwell's original technique.
A partir desse ponto, a utilização comercial da Rotomoldagem de Plástico para a produção de diversos tipos de peças teve início. Inicialmente, a Rotomoldagem era amplamente empregada na fabricação de peças com finalidades industriais, como tanques de combustível, componentes para as indústrias automobilística e agrícola, e recipientes de armazenamento. Com o tempo, o processo foi se ampliando para outros setores, como o de brinquedos, móveis, equipamentos esportivos, entre outros.
Com a popularização da rotomoldagem, essa técnica tornou-se amplamente utilizada em uma variedade de aplicações.
Popularization of rotational molding
The process of rotational molding gained popularity over the years due to its advantages, such as the ability to produce large-sized parts with complex shapes without the need for expensive molds.
With the advancement of technology and the development of new materials and equipment, rotational molding underwent constant improvements over the decades, resulting in increased efficiency, quality, and versatility in the production of plastic parts.
Rotomolding today
Currently, rotational molding is a widely used manufacturing technique in various industry sectors, such as automotive, agricultural, packaging, toys, furniture, among others.
It is considered an economical and sustainable option for the production of plastic parts due to its efficiency and low material waste.
MAIN INDUSTRIAL SECTORS THAT USE ROTATIONAL MOLDING
Rotational molding is widely used in various sectors of the modern industry. Due to its flexibility, it allows the production of resistant and durable materials.
It has been extensively used to manufacture boats, industrial tanks, customized furniture, vehicle parts, leisure market products, and consumer goods.
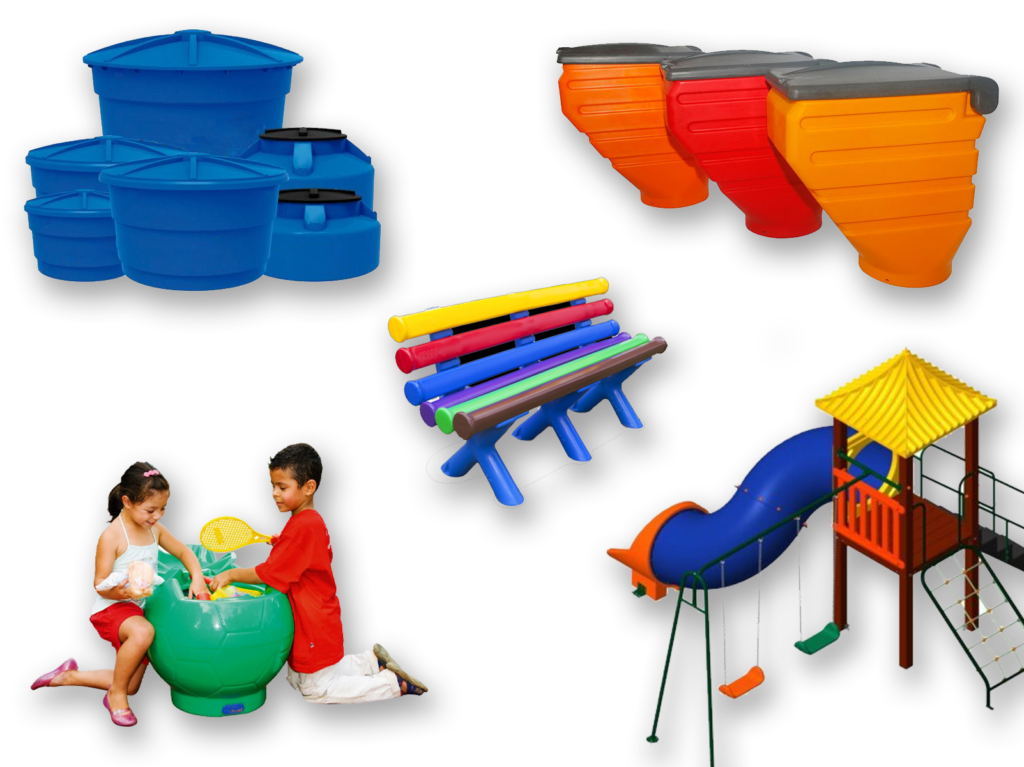
Toys
The toy industry also benefits from plastic rotational molding to produce dolls, cars, battery-powered vehicles, building blocks, and other types of toys.
The use of this technique has become popular not only in the aforementioned sectors but also extends to medical equipment, food storage, and other industrial products.
Each year, the demand for products created through rotational molding increases, as its benefits and applications are extensive.
ROTATIONAL MOLDING PROCESS
Plastic rotational molding, also known as rotomolding or rotational molding, is a manufacturing process widely used for plastic products.
Plastic rotational molding is ideal for producing hollow and relatively large products, such as fuel tanks, storage containers, mailboxes, among others.
Material Preparation
The rotational molding process begins with the preparation of the plastic material. The plastic is first granulated and/or ground to ensure uniform-sized particles.
Em seguida, a equipe combina as partículas com aditivos, como pigmentos e agentes de liberação, de acordo com o projeto do produto.
Material in the Mold
A seguir, colocamos o material misturado dentro de um molde, que representa a forma desejada do produto. Em seguida, rotacionamos o molde de forma a garantir que o plástico seja distribuído uniformemente dentro da cavidade.
Heating in the Rotational Molding Machine
Once the plastic is evenly distributed, the part is heated and cured at a specific temperature and for a defined period of time. The time and temperature of the curing process vary depending on the type and hardness of the plastic.
Cooling
Após essa etapa, resfriamos o molde à temperatura ambiente e/ou com a ajuda de ventiladores de resfriamento para que o plástico se solidifique na forma desejada.
Finished Product
Finally, the finished product is removed from the mold cavity and is ready for use. The rotational molding process is an efficient and economically viable way to produce high-quality plastic products.
In the video below, you can see more about the rotational molding process.
PARAMETERS FOR ROTOMOLDING MACHINES
Plastic Rotomolding is a specialized process that requires a high-quality rotomolding machine to produce consistent plastic articles.
Most rotomolding machines use important parameters to determine the size and quality of the final piece.
These parameters include, for example, the material used, oven temperature, rotation speed, and other variables.
Material
The material used is perhaps the most important parameter in determining how the Rotomolding machine will work.
The material can range from recycled materials to special materials that will require more complex processes. In other words, the type of material chosen for molding will determine its cost, performance, and durability.
Temperature
The oven temperature is also an important parameter. If the mold is not at the appropriate temperature, the rotomolding process will not be successful.
In other words, the oven temperature can also affect the quality of the final product. If the temperature is too high, there may be increased shrinkage, deformation, or premature hardening of the material.
Rotation Speed
Rotation speed is also an important parameter for Plastic Rotomolding. The rotation speed helps determine the size and shape of the final product.
ADVANTAGES OF PLASTIC ROTOMOLDING
This technique has numerous advantages, such as the ability to produce large volumes of products, low unit costs, and complex parts with high quality.
Here are some of the key advantages of Plastic Rotomolding.
Low Unit Costs
Due to the manufacturing process and simplicity of the technique, the unit costs are much lower compared to other manufacturing processes.
High Production Volume
Plastic Rotomolding is capable of producing large volumes of products quickly and effectively.
Product Variety
Esta técnica permite a produção de uma variedade de produtos, como recipientes, caixas, tanques, e muito mais. Além disso, é possível produzir peças complexas e com formas únicas.
High Quality
By using high-quality plastic materials, Plastic Rotomolding allows for the production of durable and high-quality products.
Finishes
Plastic Rotomolding also allows for the application of different finishes such as painting, engraving, stickers, and others.
GREATER STRENGTH
Plastic rotomolding is one of the most versatile and durable methods of plastic material production. In other words, rotomolded parts have high strength, and additional reinforcements can be added to the molded part to further enhance its integrity.
Various Applications
Devido à sua alta resistência, muitos tipos de instalações utilizam essas peças, como vasos de jardim, caiaques de lazer, tanques de óleo diesel, tanques de água e muito mais.
Furthermore, parts produced through plastic rotomolding are impact-resistant, UV-resistant, weather-resistant, and resistant to high temperatures.
TEMPERATURE INSULATION
Temperature insulation is very important for plastic rotomolding as it maintains the stability of the melted material's temperature. The plastic rotomolding process involves heating a solid polymer to form it into a mold.
Strict Control
The processing temperature needs to be strictly controlled to ensure the final product has the required sharpness and finish.
Good thermal insulation during heating is essential to prevent temperature loss, ensuring the quality and efficiency of plastic rotomolding.
PLASTIC PREPARATION
Para a Rotomoldagem de Plástico, é necessário preparar o plástico antes do processo.
Isso envolve pulverizar o material em pó inicialmente e, em seguida, aquecê-lo em um forno até que alcance seu estado típico de alta viscosidade. Após essa etapa, é essencial resfriar o material derretido dentro do molde antes de removê-lo.
This allows for efficiently obtaining unique parts without the need for complicated tools.
ABILITY FOR COMPLEX SHAPES
Plastic rotomolding is known for its ability to create plastic parts with complex shapes.
Isso porque, devido à natureza do processo de rotomoldagem, que permite que os plásticos se aqueçam e preencham completamente formas complexas, girando uniformemente e fluindo como um líquido.
Essa versatilidade é uma das principais razões pelas quais muitas aplicações de plástico escolhem a Rotomoldagem.
Cooling
A rotomoldagem de plástico conclui quando aplicamos centralmente a camada de plástico derretido ao molde e movemos lentamente o molde ao redor do eixo.
Uma vez que criamos a forma desejada, o próximo passo é o resfriamento. Durante esse processo, retiramos o molde do forno quente e o colocamos em uma câmara de ar para resfriar.
Cooling time
O tempo de resfriamento varia com base no material plástico e no tamanho do produto.
Após criar a forma desejada, retiramos completamente o produto do molde antes de colocá-lo à venda.
DEMOLDING AND FINISHING OF THE PIECE
Após a conclusão da peça, é possível realizar os processos de desmoldagem e acabamento.
These may include trimming, cutting, polishing, and painting the components, according to the customer's preference. The components are then assembled to create the final product.
Conclusion
Plastic rotational molding is a versatile molding process that provides comprehensive solutions for various sectors, from water storage containers to various industrial utensils and equipment.
Its corrosion resistance and low maintenance cost make the process highly useful for various plastic applications. Moreover, the high level of customization possible with the process is extremely beneficial for diverse industries.
In summary
Plastic rotational molding not only offers great advantages such as increased resistance, temperature insulation, and the ability to create complex shapes, among others, but also allows for greater flexibility in creating customized plastic parts.
Considering the benefits and versatility of this process, it becomes evident how useful plastic rotational molding is for manufacturing various items. If you are considering the benefits of plastic rotational molding for your production, it is advisable to consult with appropriate suppliers to find the best solution for your needs.